Dry Gas Seal: 2025 Guide to Structure and Performance
Dry gas seals are advanced sealing solutions for centrifugal compressors, offering superior performance over traditional mechanical contact seals. For example, they eliminate the need for complex oil systems, reducing leakage and wear. Therefore, this guide explores the structure, working principles, and maintenance of dry gas seals to ensure optimal performance in 2025. Learn more at John Crane’s Homepage.
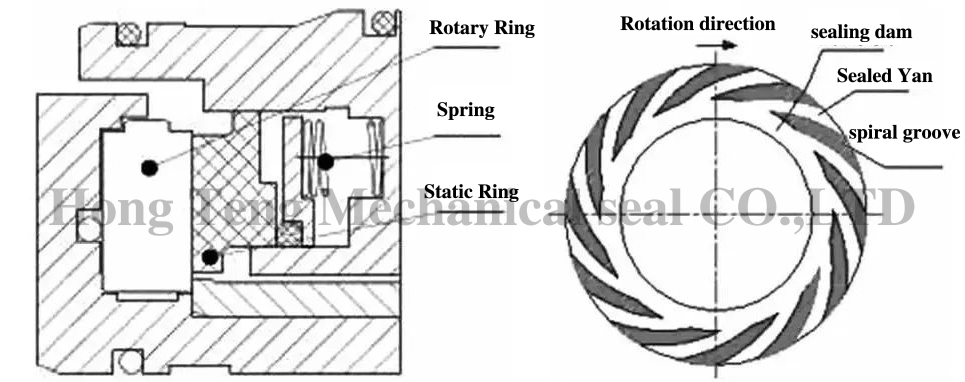
Understanding Dry Gas Seal Structure
Dry gas seal technology consists of dynamic and static components. Specifically, the stationary part includes a static ring (main ring) sealed with an O-ring, a loading spring, and a stainless steel clamping sleeve fixed in the compressor casing. In contrast, the dynamic ring (mating ring) is mounted on the rotating shaft with a clamping sleeve and locking nut for axial positioning. For instance, dynamic rings are typically made of tungsten or silicon carbide for high hardness and wear resistance. Additionally, spiral groove designs on the dynamic ring, with depths of 0.0025-0.01 mm, enhance sealing efficiency. As a result, this structure ensures reliable, non-contact sealing. Refer to AESSEAL’s Homepage for seal design insights.
Working Principles of Dry Gas Seals
The operation of a dry gas seal relies on balancing static and dynamic fluid pressures. For example, sealing gas is injected into the seal, creating static pressure regardless of rotation. When the dynamic ring rotates, spiral grooves shear gas from the outer edge to the center, generating dynamic pressure. Moreover, the sealing weir restricts gas outflow, increasing pressure to separate the static and dynamic rings. Consequently, a gas film forms, maintaining a 3-10 µm gap, which prevents contact and ensures elasticity. This gas film stiffness minimizes leakage and wear. Furthermore, the spring’s restoring force balances the gas pressure to maintain the gap. Check Flowserve’s Homepage for detailed principles.
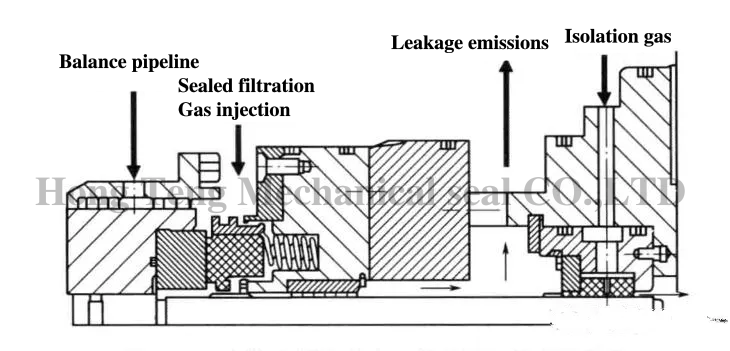
Configuration and Rotor Requirements
Gas seal technology requires precise configuration to prevent contact during rotation and ensure zero leakage when stationary. For instance, the main and mating rings must be precision-machined to maintain flatness, measured using optical strips. Additionally, the dynamic ring is secured with steps and O-rings, while the static ring is fixed in a movable clamping ring. To protect the shallow spiral grooves (a few micrometers deep), clean gas—either process gas or external nitrogen—must be filtered rigorously. This prevents contamination and maintains sealing performance. Explore Pump Industry Magazine for configuration best practices.
Auxiliary Systems for Dry Gas Seals
Unlike oil film seals, dry gas seals require simple auxiliary systems. For example, a control system monitors sealing conditions and automatic shutdowns. Clean sealing gas, such as filtered process gas or nitrogen, is injected at a higher pressure than the compressor’s process gas to prevent leakage. Additionally, a mixture of process and isolation gas is vented through a pressure switch, flow restriction orifice, and flow meter to the flare system. Nitrogen injected via a secondary inlet protects components from contamination. Before operation, clean nitrogen is used to activate and protect the sealing surface, ensuring no oil contact. As a result, these systems are less complex and costly than liquid seal setups.
Maintenance and Operational Benefits
Maintaining dry gas seals enhances their longevity, often lasting several years. For instance, regular checks ensure clean gas supply and proper filtration, preventing groove clogging. Additionally, monitoring rotor alignment and seal gap (3-10 µm) avoids frictional heat. Dry gas seals offer low leakage, minimal wear, and power consumption about 1/20th of mechanical contact seals. Moreover, they are less sensitive to rotor movement or gas properties, ensuring reliable operation in petrochemical applications. Regular maintenance, such as inspecting O-rings and springs, further extends seal life.
Conclusion
In summary, dry gas seals provide efficient, low-maintenance sealing for centrifugal compressors. By leveraging spiral groove designs, balanced pressures, and simple auxiliary systems, they ensure minimal leakage and long-term reliability. For optimal performance in 2025, follow precise installation and maintenance practices. For further guidance, consult industry resources or sealing experts.